It is no secret that historically the textile industry has made some missteps when it comes to sustainability. At Supreme, we want to change this narrative, we want to be the leaders in an industry that supports the environments we work in and the communities we work with.
So, to make our vision of the future a reality, we have adopted strategies and innovative technologies to manage our water use. We have also implemented processes and tools to mitigate toxic inks and dyes and create a circular system, in which the resources we use are given back to the Earth. Part of this system is the installation of an effluent water treatment plant. Implemented with the aim of improving our wastewater management, our effluent water treatment plant is already helping us to ensure that our quality textiles leave a positive impact on the world.
By championing and protecting people and the planet, our textiles stand for a better tomorrow and an industry that celebrates the hands that create our beautiful products and cherishes the incredible part of the world they are made in.
Sustainable Manufacturers in a Managed Sector
The textile industry doesn’t have to be the environmental villain that it is often made out to be, we are showcasing how the textile sector can work for people and the community. A core part of this is how we manage water waste and inks and dyes used in production, because contrary to how many companies act, these things can be managed.
For all our printing processes we use non-toxic REACH standard inks and dyes. However, we didn’t want to stop there so we have installed effluent treatment plants (ETP) in our factory in Pondicherry, South India.
Nestled by the Indian Ocean and in an area of incredible natural beauty, our factory works to protect the rights of workers and the delicate eco-system in which it is located. Part of our commitment to protecting the environment and workers’ health is our shiny new ETP.
Our Sustainable Factory’s Effluent Treatment Plant
Now, it is no surprise that many of us out there won’t be up to speed on the latest technology that goes into inks and dyes and water purification in the textile sector. Don’t worry we have it covered. Water treated within an ETP goes through a few distinct steps to make it safe to release back into the environment.
First, the effluent water, or wastewater, must be collected into a tank, from there it passes through a multi-grade filter. Once filtered, this water is mixed in an ozone generator. This is perhaps one of the most vital steps because this is where lime, ferrous sulphate and other common textile industry inks and dyes are eliminated. When you consider that compounds such as ferrous sulphate are toxic to aquatic life, then taking it out of the water becomes all the more important. The ozone mixer is so effective that it can remove all hazardous sludge and create no residue.
This shiny, clean, ozone polished water is then pumped through sand and activated charcoal to make sure we get all the nasties out, and then collected in a tank. The final stage is then, quite simply, using this clean water to nourish the hundreds of plants we have surrounding our factory.
Because they don’t create by-products, these systems distinctly differ from traditional chlorine-based treatment processes. An ETP system also has the advantage of taking less time and in turn, less energy, than its chlorine-based counterpart.
Why Do We Need a Sustainable Factory?
Over the past twenty years textile production has been booming, largely driven by a changing consumer approach towards increased consumption. However, as textile production has been booming so has the environmental toll that has come with it. In the Dhaka watershed, the textile industry is the second largest contributor to industrial wastewater. Meanwhile, 20% of worldwide wastewater comes from fabric dyeing and treatment, and every year the fashion sector consumes enough water to meet the needs of five million people. This needs to change.
If water goes untreated and released into the environment the impacts are far-reaching and devastating. From inhibiting plant growth to promoting toxicity to causing cancer, the impacts can be felt throughout entire ecosystems and communities.
Effluent treatment plants provide a viable way to meet textile demand without sacrificing environmental stability. By creating a circular system in which water can be treated and put back into the environment, the impact our textile factory has on the world around it is mitigated.
The Attitude of an Ethical Manufacturer
Supreme is a sustainable textile manufacturer that stands for people and the planet. Installing ETP technology is about more than protecting the environment, it is about protecting people as well. The impact of wastewater and inks and dyes sludge on local communities can be devastating.
Unethical factories commonly release untreated effluent from the textile industry back into the environment where communities live. When this wastewater contaminates the water sources that people rely on, the effect can be devastating. Everything from cancer to birth defects, blindness to skin irritation can be caused when inks and dyes are left to wreak havoc on the community.
As an ethical manufacturer, we don’t stand for this destruction. Both our use of non-toxic printing inks and dyes and our installation of the ETP means that any water we release back into the environment won’t damage the environment. It also means that it won’t cause harm to the communities that rely on this environment to survive.
A Sustainable Textile Manufacturer
As a sustainable textile manufacturer, Supreme is committed to not only creating beautiful textiles for our clients but also creating a positive impact. Our effluent treatment plant in our Pondicherry factory helps us to create this positive impact. By turning wastewater into water that can be used to help the trees surrounding our factory grow, we are creating a lasting impact and taking a stand for environmental sustainability in the textile sector.
A System that Gives Back to the Earth: Water Management at Supreme Creations
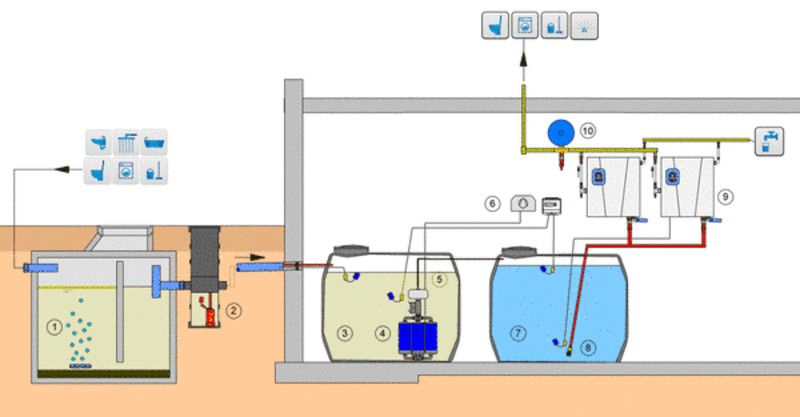
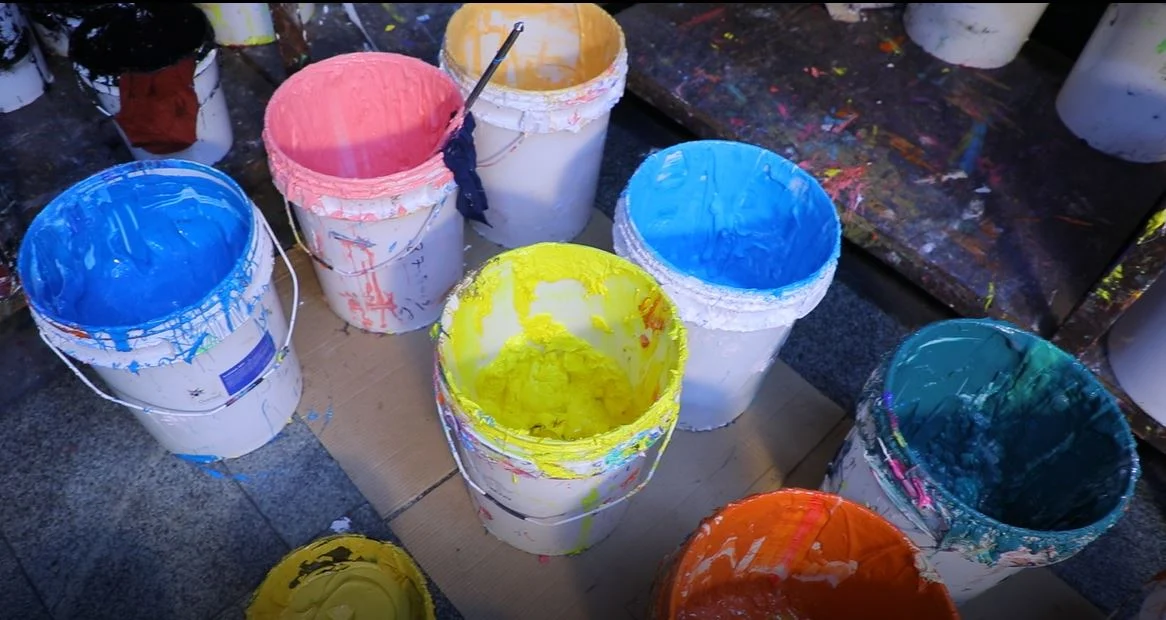